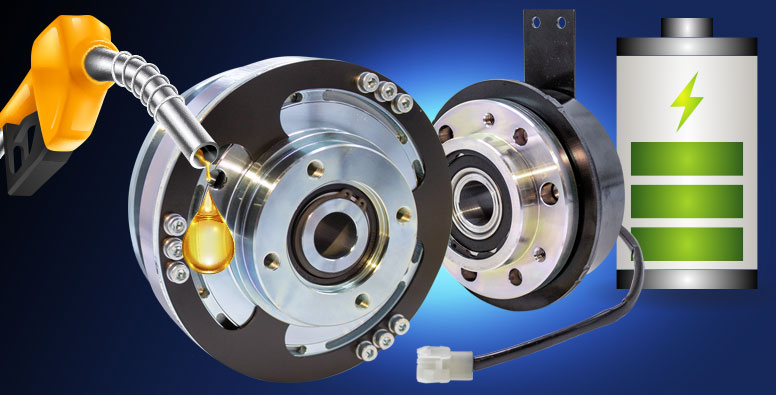
How do I connect an engine and motor/generator on a hybrid system?
Electromagnetic clutches for hybrid systems
Evolving from engine driven operation to full electric powered status takes an enormous design effort. There are also challenges to technology, component price and availability, consumer readiness, as well as regulatory hurdles along the way. For some, the decision arises to make a hybrid version until full electric can be achieved. This occurs in a wide range of applications including construction equipment, boats, electric vehicles, agricultural equipment, and more.
Construction equipment is one example. Combustion engines still provide a reliable source of power. When a machine is operated indoors, for health reasons it is advantageous to run on the electric motor only. Or, if you have both an electric motor and a combustion engine, the motor can work to assist the engine with more power when needed. Hybrid boats are the essentially the same. When out to sea, it may be best to cruise on full engine power, but while in harbor, the electric drive might be preferred.
But how is the connection between the engine and motor achieved?
General purpose clutches have long history of applications in the outdoor power equipment market. They've been put up against some of the harshest environments like salt and fertilizer spreaders. They've operated in extreme climates. Most commonly, these clutches mount directly on the engine shaft and the output drives something like a pump, cutting tool, auger or similar rotating device. In the case of a hybrid machine, the clutch is mounted as an on/off connection for the engine and motor/generator. The clutches come in several output varieties. The hub output is used for inline applications by mounting a flexible coupling half to it. For belt driven applications, a pulley is mounted to the hub, and some clutches are factory fitted with a particular pulley type. Ogura General Purpose clutches are rated for 110 to 400 lb-ft static torque. These are directional clutches so running them in reverse calls for a de-rating so that the internal leaf springs are not put into compression and damaged.
If full torque is required in each direction, a bi-directional clutch such as Industrial or Mobile clutch model MMC is used. These are heavy duty clutches, with torque ratings up to 1,500 lb-ft and built to withstand outdoor environments and heavy vibration. They also are easily driven by universal drive shafts, as the bolt pattern on the universal hub matches up with common drive shaft couplings. MMC clutches are prevalent in the commercial fishing industry where they used to run the hydraulic pumps. MMC clutches also have a limp home feature where the clutch can be mechanically locked in the engaged position if a problem arises out at sea or in the middle of an important job on land.
Benefits of using an Ogura mobile and general purpose clutches:
- Long life
- Safety and convenience with remote starting
- Fuel and energy savings
- Built for outdoor operation
- Many years of proven success
- Custom designs available based on minimum order quantities
- Reduced engine load on cold weather starts
- Increased operational life of driven equipment
- Lower fuel consumption
- Available with a soft start controller
- Slip detect capability
- Simple installation