Troubleshooting Electromagnetic Clutches and Brakes
Clutch Will Not Disengage
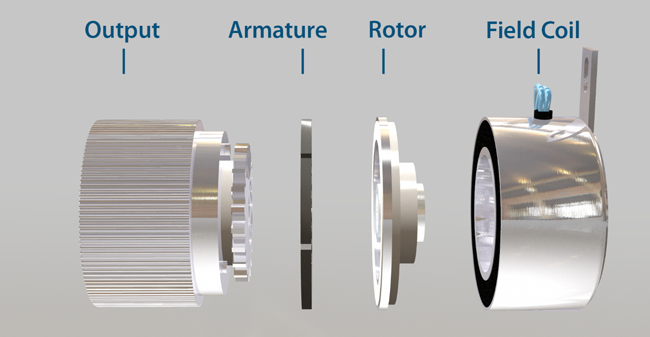
This 22 minute video will help you on your way to troubleshooting electromagnetic clutch and brake issues. The video is conveniently broken down into sections. You can jump to "Will not disengage" at 9:55
Potential Problem | Possible Reason | Solution |
---|---|---|
Voltage not releasing. | Faulty switch. | Replace switch. |
|
The clutch has been severely galled and has locked up. (Galling is the condition whereby a piece of metal is trapped between the armature and the rotor and melts due to high pressure and heat, spot welding the surfaces together.) | If rotor and armature cannot be separated, replace the clutch. If they do separate, follow burnishing procedure. |
Pulley bearing locked. |
Bearing lost grease due to seal problem, temperature or water contamination. (Example) |
Replace clutch. |
Voltage is going to the clutch but the clutch will still not engage. | The air gap is too large. (Example) | If straight bore the air gap can be readjusted. If unit has set screw, bottom out armature hub against field then back off to 0.1 inches and re-tighten set screw. If spacers are used on straight bore reduce the width of the spacer. If its a taper bore clutch tap on the armature cover plate to close air gap. |
Clutch Will Not Engage
This 22 minute video will help you on your way to troubleshooting electromagnetic clutch and brake issues. The video is conveniently broken down into sections. You can jump to "Will not engage" at 4:21
Potential Problem | Possible Reason | Solution |
---|---|---|
No voltage going to the clutch. | Wiring connector not seated properly. | Pull apart and re-seat connector. |
No voltage or low voltage coming from the battery. | Check with voltmeter, battery should be 8-16 volts. (Assuming 12 volt battery.) | |
Defective charging system. | Fix charging system. | |
Lead wire cut or broken internally. (Example) | Fix or replace lead wire. If destroyed, replace clutch. | |
Fuse blown. | Replace fuse. | |
Defective switch operating clutch. | Replace the switch. | |
If voltage is going to the clutch, but the clutch will still not engage. | Coil open or shorted. | Check coil with ohmmeter. A range close to 3 to 4 ohms should be present at an ambient coil temperature of 70\uffffF. Replace coil. (Example) |
Check coil voltage to make sure it is compatible with the voltage coming in. (If voltage is too high, this could cause the coil to burn out.) | Change battery or coil to meet your requirement. | |
Burnt out coil caused by frictional contact (rotor strike). If so, coil will be discolored, can be cracked, burnt or epoxy can be melted. (Example 1, Example 2) | Replace coil. | |
Clutch engages, but load will not engage. | Rivets or springs broken. (Example) |
Replace clutch. |
Key missing. | Put in key. | |
Armature could be warped because of heat due to slippage. This means it will pull in, but will slip when a load is supplied. Clutch should show signs of heat. (Example) | Replace clutch and determine why it slipped. |
Clutch Slips
This 22 minute video will help you on your way to troubleshooting electromagnetic clutch and brake issues. The video is conveniently broken down into sections. You can jump to the following sections that deal with slippage:
Excessive slipping - 16:45
Excessive slipping from electrical - 17:19
Excessive slipping from contamination - 18:32
Excessive slipping from the application or lack of burnishing - 19:08
Potential Problem | Possible Reason | Solution |
---|---|---|
Low voltage going into the clutch. | Defective battery. | Check with voltmeter, battery should be 8-16 volts. (Assuming 12 volt battery.) |
Lead wire cut which could be intermittently grounding out the lead wire causing the clutch to turn on and off or not to give full voltage. (Example) |
Fix or replace lead wire. | |
Erratic engagement. | If lead wire is kinked or pinched and the break is internal, the clutch operation may show up as being erratic engagement. (Example) |
Fix or replace lead wire. |
Clutch is contaminated. | Oil or other lubricant has been sprayed on the clutch surface. Sometimes this shows up after the clutch is disassembled. Physical evidence is either burnt oil or a greasy metallic surface showing oil still present. (Example) |
Clean off surfaces with solvent and re-burnish. Replace the clutch if damage is severe enough. |
Clutch overloaded. | Output torque required is greater than what the clutch can handle. If input torque going into clutch is greater than the output torque required, the clutch will slip. If it slips too long, the clutch surfaces will be galled | Size clutch correctly for the application. Replace clutch. |
Output stalled. | If output is stalled, clutch could slip to the point where it will burn up and destroy either bearings or the field. | Replace clutch. |
If voltage is going to the clutch, but the clutch will still not engage. | Coil open or shorted. | Check coil with ohmmeter. A range close to 3 to 4 ohms should be present at an ambient coil temperature of 70\uffffF. Replace coil. |
Clutch not burnished. | If full torque is required immediately and clutch is not burnished, it will slip and could become galled. | Try to re-burnish clutch. If slipping is to severe, clutch will have to be replaced. |
Noisy Clutch
This 22 minute video will help you on your way to troubleshooting electromagnetic clutch and brake issues. The video is conveniently broken down into sections. You can jump to the following sections that deal with Noise:
Noise - 11:47
Noise - armature/hub - 12:34
Noise - bearings - 13:33
Noise - rotor contact - 15:42
Potential Problem | Possible Reason | Solution |
---|---|---|
If clutch is able to move on the shaft. | Check center bolt and washer to make sure it is tight. If it is tight, make sure that the shaft is not too long. Clutch shaft should end before the end of the clutch to allow some deflection in the center bolt and washer to keep clutch on tightly. (Example) | re-tighten center bolt or change spacer or shaft length. |
Noise from pulley bearing. | Check if bearing feels rough. Check belt load to make sure pulley and bearings are not over loaded. | Reduce belt load. |
High temperature can be caused by either operating environment or due to slippage. If slippage, clutch should be discolored. Refer to slippage section for potential reasons. | Reduce the heat or eliminate slippage. | |
Pinging or scraping noise noticed when clutch is disengaged | Air gap too close. (Example) | Increase air gap. |
Surface is heavily galled. | Re-burnish the clutch. | |
Noise from field bearing. | Check to see if the clutch is discolored to see if it shows signs of slippage. | Refer to slippage section. |
Check to see if the clutch is discolored to see if it shows signs of slippage. | Refer to slippage section. | |
Check for damage to both the outer race and inner race of the bearing. Make sure key is not too tight forcing pressure on the inner race . In the outer race area, check for marks or damage that could have caused the clearances to close up. (Example 1, Example 2, Example 3) | Replace clutch. | |
Check temperature of shaft where clutch is mounted to verify that it is under 300°. | Reduce reason for the high temperature overloading on the engine. | |
Check torque tab or backing plate to make sure that there is freedom of movement of 1/16 of an inch axially and radially. Check to see if any marks are evident that would indicate axial forces applied. (Example) |
Loosen torque tab to make sure it has freedom of movement both axially and radially. | |
Noise is evident when the clutch is first installed and rotated by hand. | 1. Possible causes are bolts holding the field are not tightened down properly. | 1. Tighten bolts |
2. Key in key way is not seated properly. This could cause the clutch to cock to one side. | 2. Remove rotor assembly and reset key way. | |
3. Lead wire is pinched between mounting face and field bracket cocking field assembly. | 3. Loosen the bolts, remove the wire and re-tighten the field mounting bolts. | |
4. If set screw version, this could be because of improper air gap between pulley/armature and field. | 4. Push together, then back off .1 inches and re-tighten set screw. | |
5. Mounting face in not concentric with shaft. | 5. Remachine mounting holes or switch mounting face (by switching you are able to verify if mounting holes on the clutch are the problem or the mounting holes on the face are the problem.) | |
Mounting bracket has come loose from the back of the field assembly. | Check to see if projection wells are broken. If they are check to see if rotor strike has occurred. Possible misalignment in combination of belts and side load can break projection wells. (Example) | Replace the clutch |